在工業生產的廣闊版圖中,局部高頻加熱淬火熱處理技術憑借其卓越的特性,成為金屬零件表面硬化處理的中流砥柱。這項技術在齒輪、軸類、刀具、模具等眾多關鍵工件的加工中廣泛應用,為提升它們的性能與延長使用壽命立下汗馬功勞。
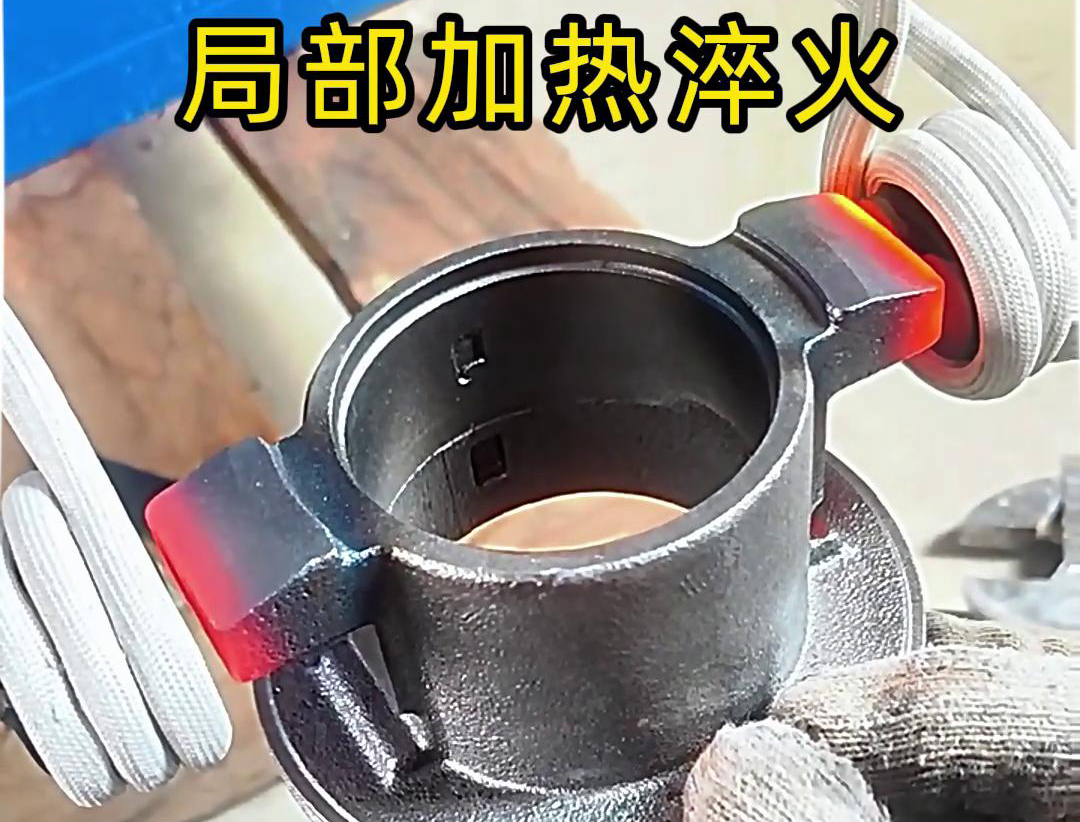
局部高頻加熱淬火熱處理基于電磁感應原理。當高頻電流通過環繞金屬零件的感應線圈時,瞬間產生高頻交變磁場。處于該磁場中的金屬零件,因其導電特性,表面會產生感應電流(渦流)。由于集膚效應,電流主要集中在零件表面,使表面迅速發熱升溫。當達到合適的淬火溫度后,立即進行快速冷卻,實現零件表面的硬化處理,而內部仍保持較好的韌性。
- 高效快速:高頻加熱速度極快,能在極短時間內將零件表面加熱到淬火所需溫度。與傳統加熱方式相比,可大幅縮短生產周期。例如,傳統加熱方式可能需要數十分鐘將零件加熱到合適溫度,而高頻加熱僅需數秒到數分鐘,顯著提高了生產效率,滿足大規模生產需求。
- 精準控制:可精確控制加熱區域和溫度。通過設計感應線圈的形狀、尺寸以及調整高頻電流的參數,能精準地對零件特定部位進行加熱,實現局部淬火。同時,借助高精度溫度控制系統,溫度控制精度可達 ±5℃,確保每次淬火質量的穩定性和一致性。
- 節能降耗:熱量集中在零件表面產生,能量利用率高,減少了熱量向周圍環境的散失,相比傳統加熱方式,可節能 30% - 50%,降低生產成本,符合現代工業節能環保的發展趨勢。
- 提升性能:經過局部高頻加熱淬火后,零件表面形成高硬度的淬硬層,顯著提高耐磨性、抗疲勞性和耐腐蝕性等性能。而零件內部仍保持較好的韌性,使零件具備良好的綜合機械性能,延長使用壽命。
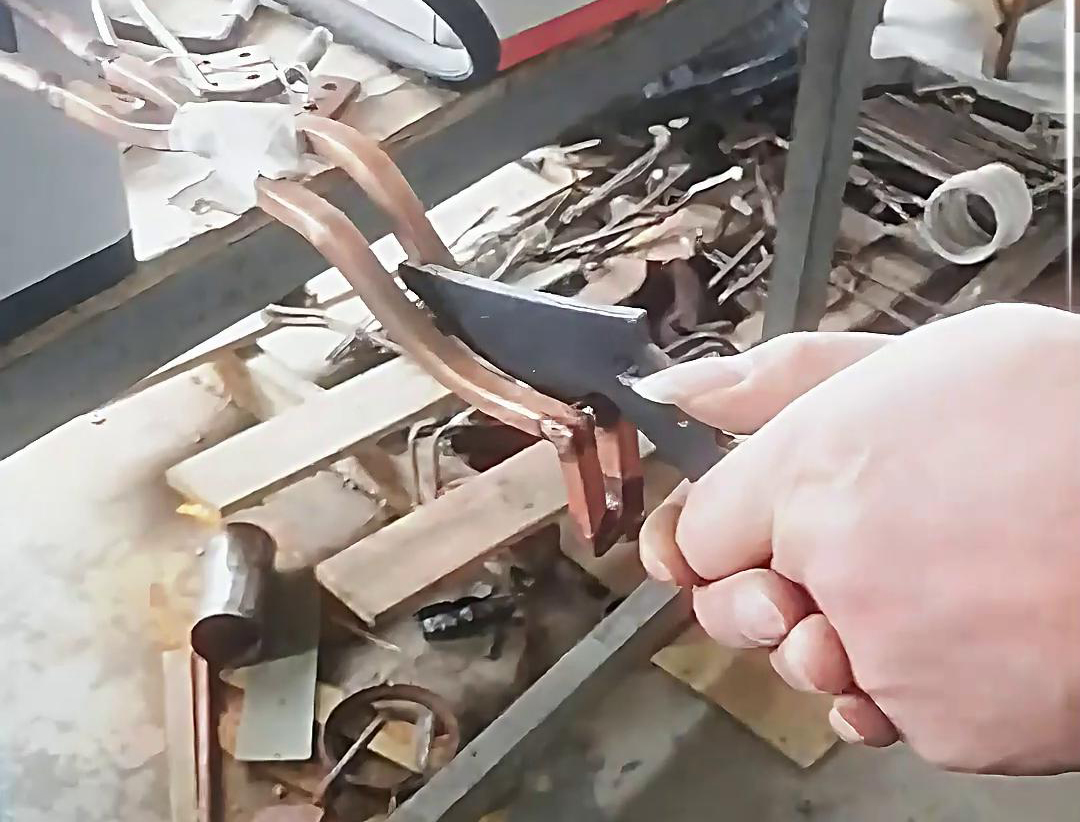
- 性能提升:在汽車、機床等設備中,齒輪工作時承受著交變載荷和摩擦。通過局部高頻加熱淬火,齒輪齒面硬度大幅提高,一般可從 HRC20 - 30 提升至 HRC50 - 60,有效增強齒面耐磨性,減少齒面磨損和疲勞點蝕的發生。同時,齒輪心部保持足夠韌性,防止在高負荷下發生脆性斷裂,提高了齒輪的承載能力和使用壽命,確保設備穩定運行。
- 應用特點:根據齒輪的模數、齒數、材質等因素,精確調整高頻淬火參數。對于大模數齒輪,適當增加加熱功率和時間,保證足夠的淬硬層深度;對于小模數齒輪,嚴格控制加熱參數,避免過度淬火導致齒面開裂。通過定制化的淬火工藝,滿足不同工況下齒輪的性能要求。
- 性能提升:軸類零件在旋轉過程中,表面與其他部件接觸產生摩擦,同時承受一定的彎曲、扭轉等載荷。局部高頻加熱淬火使軸表面形成硬而耐磨的淬硬層,提高軸的耐磨性和抗疲勞強度。例如,發動機曲軸經過高頻淬火后,表面硬度提高,能夠更好地抵抗活塞連桿的沖擊和摩擦力,減少磨損,延長曲軸的使用壽命,保證發動機的可靠性和耐久性。
- 應用特點:針對軸類零件不同部位的受力情況,進行局部選擇性淬火。如軸頸部位,因與軸承配合,承受較大摩擦力,對耐磨性要求高,可進行較深的淬硬層淬火;而軸的其他部位,根據實際需求調整淬火深度和硬度,實現軸類零件性能的優化設計,在滿足使用要求的同時,降低生產成本。
- 性能提升:刀具在切削過程中,刃口需要承受高溫、高壓和強烈的摩擦。局部高頻加熱淬火使刀具刃口獲得高硬度和耐磨性,一般刃口硬度可達 HRC60 以上,提高刀具的切削性能和耐用度。同時,刀具基體保持較好的韌性,防止在切削過程中刃口崩裂,延長刀具的使用壽命,提高加工效率和產品質量。
- 應用特點:根據刀具的材質、形狀和加工要求,靈活調整高頻淬火工藝。對于高速鋼刀具,通過精確控制加熱溫度和冷卻速度,使碳化物均勻彌散分布,提高刀具的紅硬性;對于硬質合金刀具,采用適當的高頻淬火參數,在保證刃口硬度的同時,避免因淬火應力導致刀具出現裂紋等缺陷。
- 性能提升:模具在成型過程中,表面承受著巨大的壓力、摩擦力和熱疲勞。局部高頻加熱淬火提高模具表面硬度和耐磨性,增強模具的抗熱疲勞性能,減少模具表面的磨損、拉傷和熱裂紋的產生,提高模具的使用壽命和成型零件的質量。例如,壓鑄模具經過高頻淬火后,表面硬度提高,能夠承受更高的溫度和壓力,生產出的壓鑄件尺寸精度更高,表面質量更好。
- 應用特點:根據模具的類型、尺寸和使用工況,制定個性化的高頻淬火方案。對于大型模具,采用分段淬火或分區淬火的方式,保證模具各部位的淬火質量;對于復雜形狀的模具,通過設計特殊形狀的感應線圈,實現對模具關鍵部位的精準淬火,滿足模具不同部位的性能要求。
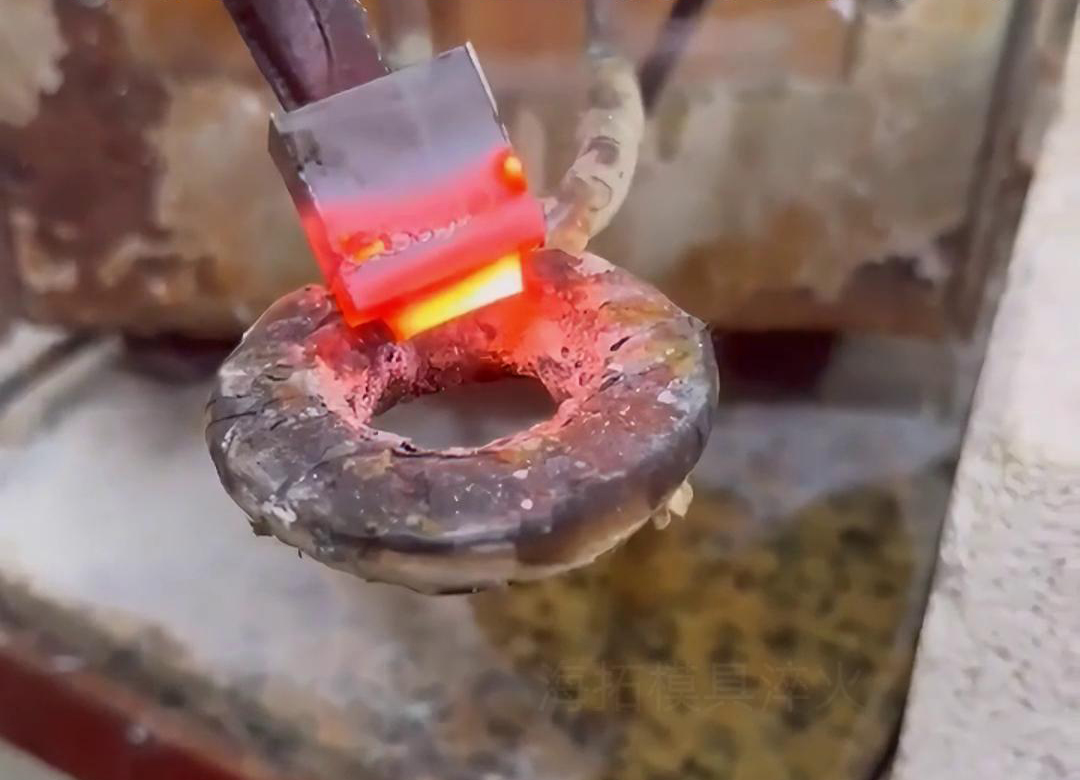
局部高頻加熱淬火熱處理技術以其獨特的優勢,在工業領域的金屬零件加工中發揮著不可或缺的作用。隨著工業技術的不斷進步,這項技術將不斷創新和完善,為提高金屬零件性能、推動工業高質量發展提供更強大的支持。